乙炔气柜隐患探析
2015/12/21 9:10:24 点击: 文章来源:www.jshhcc.com
1 乙炔装置 2R200 裂化气气柜使用状况四川维尼纶厂乙炔装置 2R200 裂化气气柜( 10 km3) 是天然气制乙炔技术中的关键设备,它在生产运行中起着裂化气储存与负荷平衡作用。该气柜于 1979 年 11 月投用至今已 32 年了,为确保该气柜安全、稳定、长周期运行,川维厂曾在2007、2008 和 2010 年 3 次装置系统停车大修期间,连续3 次对该气柜进行了清淤、检测和缺陷处理,但在2010 年最近一次对气柜检测检修时发现:
( 1) 该气柜的钟罩、中间升降槽( 上、下) 筒体与密封水接触部位的壁板,多处出现腐蚀穿孔与坑蚀减薄,中间升降槽( 上、下) 筒体及钟罩壁板也存在变形。在坑蚀深度在1 mm 以上的坑点达100多个,有的坑点深度达到 2 mm,并出现有 8 处穿孔( 均在中间升降槽下筒体) ,严重威胁安全生产。
( 2) 中间升降槽( 上、下) 筒体人孔附近坑蚀严重,大部分壁板大面积腐蚀减薄。( 3) 气柜中部分定位导轮出现损伤、腐蚀和导轨变形; 操作平台支撑钢结构锈蚀严重,甚至有部分还穿孔破损。( 4) 气柜 2007、2008 和 2010 年修补情况见表 1。
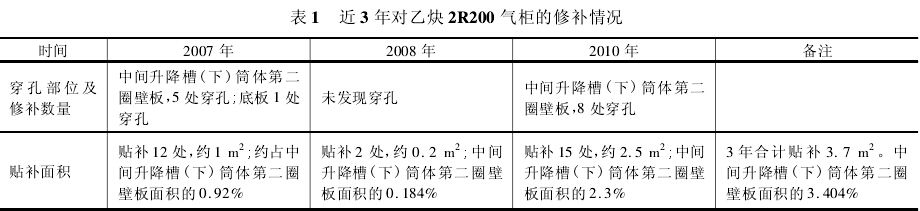
由表 1 可知,今后若再对 2R200 气柜的腐蚀采取修修补补的方式,已不能从根本上解决该气柜的严重腐蚀问题以及重大安全隐患。因此,需对该气柜实施彻底的隐患治理。
( 2) 中间升降槽( 上、下) 筒体人孔附近坑蚀严重,大部分壁板大面积腐蚀减薄。( 3) 气柜中部分定位导轮出现损伤、腐蚀和导轨变形; 操作平台支撑钢结构锈蚀严重,甚至有部分还穿孔破损。( 4) 气柜 2007、2008 和 2010 年修补情况见表 1。
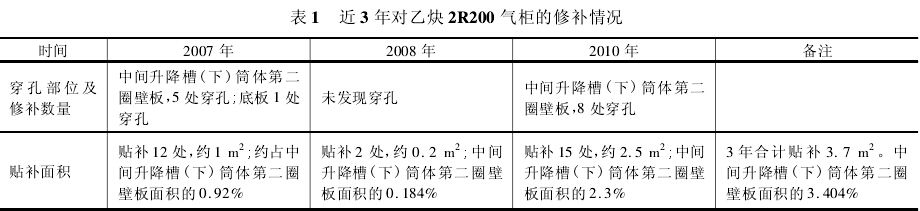
2 2R200 气柜隐患治理方案研究与比选
2R200 裂化气气柜为湿式气柜( 引进设备) ,它由下部水槽、中间升降槽( 上、下) 筒体、上部钟罩和升降轨道、操作平台及框架组成。气柜直径24. 5 m,高度 32 m,容积 10 km3,材质碳钢,气柜外框架高度达38 m。由于气柜的体积及施工工程量都很大,无法在30 天内完成该气柜的整体更新改造。
2. 1 方案一
采取提前准备、深度预制、逐级起吊、局部更换技术,对中间升降槽( 上、下) 下筒体、二带壁板圈和钟罩一带壁板圈实施更换,气柜其它部位及设施保留,工期 30 天。
( 1) 首先在气柜各级筒体上由外向内依次开孔[包括水槽、中间升降槽( 上、下) 筒体和钟罩],将起吊用立柱、更换用钢板等材料全部倒运到钟罩内,焊接就位起吊钟罩的 7 m 立柱并加固。
2R200 裂化气气柜为湿式气柜( 引进设备) ,它由下部水槽、中间升降槽( 上、下) 筒体、上部钟罩和升降轨道、操作平台及框架组成。气柜直径24. 5 m,高度 32 m,容积 10 km3,材质碳钢,气柜外框架高度达38 m。由于气柜的体积及施工工程量都很大,无法在30 天内完成该气柜的整体更新改造。
2. 1 方案一
采取提前准备、深度预制、逐级起吊、局部更换技术,对中间升降槽( 上、下) 下筒体、二带壁板圈和钟罩一带壁板圈实施更换,气柜其它部位及设施保留,工期 30 天。
( 1) 首先在气柜各级筒体上由外向内依次开孔[包括水槽、中间升降槽( 上、下) 筒体和钟罩],将起吊用立柱、更换用钢板等材料全部倒运到钟罩内,焊接就位起吊钟罩的 7 m 立柱并加固。
( 2) 对 2R200 气柜的钟罩及中间升降槽( 上、下) 筒体,用槽钢分别焊接两道胀圈( 以防止气柜各筒体变形) ; 并在气柜内侧分三圈均布 36 根临时提升立柱,作为吊装抱杆( 立柱之间用架杆、钢绳或钢管连接固定,并与中间立柱相连固定,形成网状环拉形式,以保持各立柱建立起一个稳固的网状环拉系统) 。
( 3) 在立柱上挂12 个手拉葫芦( 每个10t) ,气柜筒体采用人工起吊,按照先起吊钟罩更换其腐蚀壁板、加 5 m 立柱支撑; 再起吊中间升降槽( 上)筒体更换其腐蚀壁板、加 3. 5 m 立柱支撑; 最后起吊中间升降槽( 下) 筒体更换其腐蚀壁板。
( 4) 按先落下中间升降槽( 下) 筒体、拆除立柱,并割除焊接胀圈; 再落下中间升降槽( 上) 筒体、拆除立柱,并割除焊接胀圈; 后落下钟罩、拆除立柱,并割除焊接胀圈; 再对水槽壁板开孔及外导向轮更换等顺序对气柜进行恢复,从而完成2R200 气柜腐蚀壁板的更换工作。
( 5) 气柜焊缝在无损探伤检测合格后予以防腐,经气密、升降试验和质量评价合格后使用。
( 5) 焊接接头的装配符合设计文件和表 3 要求。
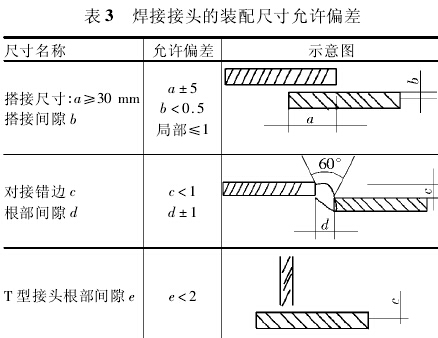
( 6) 焊接质量检验: 对气柜预制组件及新组装的中间升降槽( 上、下) 筒体壁板所有对接焊缝,均应通过煤油渗透试验; 焊缝不得有裂纹、气孔、弧坑和夹渣,咬边深度小于 0. 5 mm,连续长度小于100 mm,且总长小于焊缝长度的 10% ; 下水封焊缝注水试验,不漏为合格; 对气柜焊缝的 X 射线探伤抽检率要达到: 环焊缝不低于 5%,纵焊缝不低于 10%,丁字焊缝不低于 15%,且 X 射线探伤的一次抽检合格率应在 90%以上,按《钢制压力容器无损检测》JB4730—2005 标准 III 级为合格,不合格则按要求进行扩探,直至合格为止。( 4) 按先落下中间升降槽( 下) 筒体、拆除立柱,并割除焊接胀圈; 再落下中间升降槽( 上) 筒体、拆除立柱,并割除焊接胀圈; 后落下钟罩、拆除立柱,并割除焊接胀圈; 再对水槽壁板开孔及外导向轮更换等顺序对气柜进行恢复,从而完成2R200 气柜腐蚀壁板的更换工作。
( 5) 气柜焊缝在无损探伤检测合格后予以防腐,经气密、升降试验和质量评价合格后使用。
2. 2 方案二
采取提前准备、深度预制、模块化组装技术,对中间升降槽( 上、下) 筒体和钟罩全部实施更换,气柜水槽、操作平台及框架保留,工期 30 天。
( 1) 根据气柜周围环境,按 120 °方位均布 3台 200 t 汽车吊。
( 2) 首先将气柜钟罩拱顶上的 2 个水压保护器和脊盖板拆除,然后在钟罩内搭设 4 根中心支撑柱( 219 ×14 钢管) 及架设,中心支撑架高度为10. 355 m,长宽各为 6 m。搭设时要求立杆间距为300 mm,横杆间距为 1000 mm,层与层之间,立柱之间加设斜杆支撑,使其成为一个稳定的整体,并使其中心半径 3 m 内的立杆,必须均匀支撑住钟罩拱顶骨架中心环板,以便于旧钟罩拱顶的拆除和新钟罩拱顶的定位及安装
( 3) 将钟罩拱顶外圆按 36 °划分切割为 10 大块用大吊车吊出,然后将钟罩筒体按 10 大块等分切割吊出,依次将中间升降槽( 上、下) 筒体分别按10 大块等分切割吊出。
( 4) 将提前准备、深度预制的中间升降槽( 上、下) 筒体和钟罩筒体 10 片及其拱顶 8 片组件,按先后安装顺序运至施工现场; 然后采用模块化组装技术,依次完成中间升降槽( 下) 筒体和( 上) 筒体、钟罩筒体、钟罩拱顶的组装。
( 5) 气柜焊缝在无损探伤检测合格后予以防腐,经气密、升降试验和质量评价合格后使用。经对研究及评价比选认为,方案一和方案二均具有可行性。经利弊权衡后最终采用方案二。
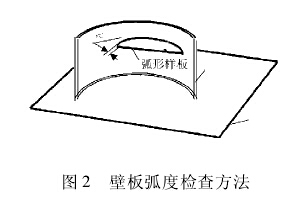
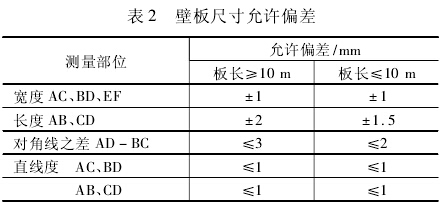
( 4) 气柜所用的槽钢圈、角钢圈其分段预制长度一般不应小于 5 m。不论采用热煨还是冷弯,都应按设计直径在平台上放样校正弧度,并检查水平翘曲度。其径向允许偏差为 ±3 mm。水平翘曲度不得大于 5 mm。其他弧形型钢与平台实样间的弧度间隙及翘曲度不得大于 4 mm。采取提前准备、深度预制、模块化组装技术,对中间升降槽( 上、下) 筒体和钟罩全部实施更换,气柜水槽、操作平台及框架保留,工期 30 天。
( 1) 根据气柜周围环境,按 120 °方位均布 3台 200 t 汽车吊。
( 2) 首先将气柜钟罩拱顶上的 2 个水压保护器和脊盖板拆除,然后在钟罩内搭设 4 根中心支撑柱( 219 ×14 钢管) 及架设,中心支撑架高度为10. 355 m,长宽各为 6 m。搭设时要求立杆间距为300 mm,横杆间距为 1000 mm,层与层之间,立柱之间加设斜杆支撑,使其成为一个稳定的整体,并使其中心半径 3 m 内的立杆,必须均匀支撑住钟罩拱顶骨架中心环板,以便于旧钟罩拱顶的拆除和新钟罩拱顶的定位及安装
( 3) 将钟罩拱顶外圆按 36 °划分切割为 10 大块用大吊车吊出,然后将钟罩筒体按 10 大块等分切割吊出,依次将中间升降槽( 上、下) 筒体分别按10 大块等分切割吊出。
( 4) 将提前准备、深度预制的中间升降槽( 上、下) 筒体和钟罩筒体 10 片及其拱顶 8 片组件,按先后安装顺序运至施工现场; 然后采用模块化组装技术,依次完成中间升降槽( 下) 筒体和( 上) 筒体、钟罩筒体、钟罩拱顶的组装。
( 5) 气柜焊缝在无损探伤检测合格后予以防腐,经气密、升降试验和质量评价合格后使用。经对研究及评价比选认为,方案一和方案二均具有可行性。经利弊权衡后最终采用方案二。
3 采用方案二的注意事项
( 1) 施工承包商对新安装的中间升降槽( 上、下) 筒体和钟罩,必须严格按照 2R200 裂化气气柜原图纸、原结构、原尺寸技术要求进行,必须满足《金属 焊 接 结 构 湿 式 气 柜 施 工 及 验 收 规 范》HGJ212—83、《石油化工立式圆筒形钢制储罐施工工艺标准》SH/T3530—2001、《现场设备、工业管道焊接工程施工及验收规范》GB50236—98、《钢制压力容器无损检测》JB4730—2005、《石油化工建设工程项目施工安全技术规范》GB50484—2008 等相关设备安装技术规范。
( 2) 通过精细放样、制作工装、深度预制,对新安装的中间升降槽( 上、下) 筒体、钟罩筒体壁板组件预制精度的测量偏差,应控制在表2 范围内,见图1。

( 3) 对壁板壁厚大于或等于 4 mm 的弧形状组件,应先进行滚圆,滚圆前应对其端部弧度要求的预弯曲进行复核检查,滚圆后应采用弦长不小于 1. 5 m 的圆弧样板进行检查,圆弧样板与预弯组件间的间隙不应大于 2 mm。见图 2。( 1) 施工承包商对新安装的中间升降槽( 上、下) 筒体和钟罩,必须严格按照 2R200 裂化气气柜原图纸、原结构、原尺寸技术要求进行,必须满足《金属 焊 接 结 构 湿 式 气 柜 施 工 及 验 收 规 范》HGJ212—83、《石油化工立式圆筒形钢制储罐施工工艺标准》SH/T3530—2001、《现场设备、工业管道焊接工程施工及验收规范》GB50236—98、《钢制压力容器无损检测》JB4730—2005、《石油化工建设工程项目施工安全技术规范》GB50484—2008 等相关设备安装技术规范。
( 2) 通过精细放样、制作工装、深度预制,对新安装的中间升降槽( 上、下) 筒体、钟罩筒体壁板组件预制精度的测量偏差,应控制在表2 范围内,见图1。

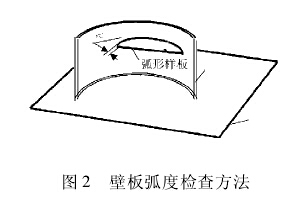
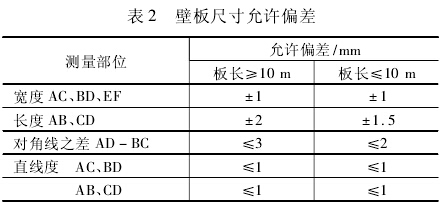
( 5) 焊接接头的装配符合设计文件和表 3 要求。
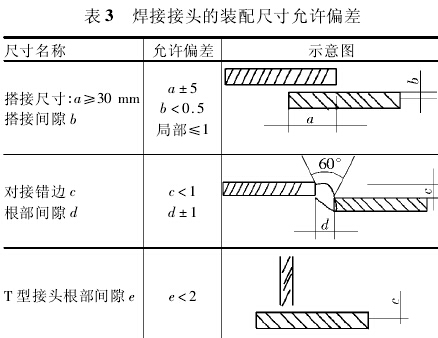
( 7) 2R200 新气柜上浮压力应严格按照原设计 0. 0035 MPa 进行取值,以使 2R200 气柜经 30多年的运行,在完全摆脱了气柜钟罩顶部、钟罩内壁和中间升降槽( 上、下) 筒体内壁附着较多聚合物后( 附着物重量约有几吨) ,以恢复 2R200 气原设计、原工况的使用状态。
( 8) 为确保 2R200 气柜钟罩的配重均衡、试验可调、节约高效、一次到位、升降自如,在气柜钟罩下部配重箱拆除时,应按对应方位的配重箱编号和称重重量。其配重块经喷砂除锈防腐后,将原配重 80%重量的配重块,装入钟罩下部对应方位及编号的配重箱内; 将另外原配重 20% 重量的配重块,按对应方位加装到钟罩顶部上面配重箱内,以此便于气柜升降试验时进行必要的平衡调配。
( 9) 2R200 新气柜升降试验应严格按照原设计要求进行,须做到: 升降缓慢、平稳,钟罩和中间升降槽( 上) 筒体,以及中间升降槽( 上、下) 筒体和筒体的密封水槽咬合要可靠,各部无泄漏; 19 m高限位报警、20 m 高限位联锁和 3. 5 m 低限位报警试验要正常; 最后两次快速升降试验的升降速
度要控制在 1. 5 m/min 范围内。
( 10) 2R200 新气柜升降试验和质量评价合格后,应按照《石油化工工程建设交工技术文件规定》SH3503—2007 标准和《石油化工工程建设施工过程技术文件规定》SHT3543—2007 标准,做好2R200 新气柜的竣工资料; 同时,应将乙炔 2R200气柜隐患治理在预制、拆除、安装及试验全过程的影像资料制作成光盘,随竣工资料一并归档备查。-------------本文由干式气柜公司整理发布,如需转载,请注明!
( 8) 为确保 2R200 气柜钟罩的配重均衡、试验可调、节约高效、一次到位、升降自如,在气柜钟罩下部配重箱拆除时,应按对应方位的配重箱编号和称重重量。其配重块经喷砂除锈防腐后,将原配重 80%重量的配重块,装入钟罩下部对应方位及编号的配重箱内; 将另外原配重 20% 重量的配重块,按对应方位加装到钟罩顶部上面配重箱内,以此便于气柜升降试验时进行必要的平衡调配。
( 9) 2R200 新气柜升降试验应严格按照原设计要求进行,须做到: 升降缓慢、平稳,钟罩和中间升降槽( 上) 筒体,以及中间升降槽( 上、下) 筒体和筒体的密封水槽咬合要可靠,各部无泄漏; 19 m高限位报警、20 m 高限位联锁和 3. 5 m 低限位报警试验要正常; 最后两次快速升降试验的升降速
度要控制在 1. 5 m/min 范围内。
( 10) 2R200 新气柜升降试验和质量评价合格后,应按照《石油化工工程建设交工技术文件规定》SH3503—2007 标准和《石油化工工程建设施工过程技术文件规定》SHT3543—2007 标准,做好2R200 新气柜的竣工资料; 同时,应将乙炔 2R200气柜隐患治理在预制、拆除、安装及试验全过程的影像资料制作成光盘,随竣工资料一并归档备查。-------------本文由干式气柜公司整理发布,如需转载,请注明!
- 上一篇:新型煤气柜的整体结构 2015/12/22
- 下一篇:造气联合过热器及洗气塔系统优化 2015/12/18